Lorem ipsum dolor sit amet...
Dry type transformers are a type of electrical transformers where the core and windings are not immersed in insulation oil but instead utilize natural cooling or forced air cooling. As an emerging power distribution equipment in recent years, dry-type transformers have been widely utilized in power transmission and distribution systems in various locations such as factory workshops, high-rise buildings, commercial centers, airports, docks, subways, and oil platforms. They can also be integrated with switchgear to form compact substation units.
Currently, dry type transformers typically operate within voltage ratings ranging from 6 to 35 kV, with a maximum capacity of up to 25 MVA. Are you interested in delving deeper into dry-type transformers? This blog post will provide a detailed exploration of their structural forms, cooling methods, types, and advantages compared to oil-immersed transformers. Additionally, the article will cover installation and commissioning, fault diagnosis through sound analysis, mitigation of noise caused by external structures, and selection criteria. By optimizing the structure, dry-type transformers can be made more efficient and reliable.
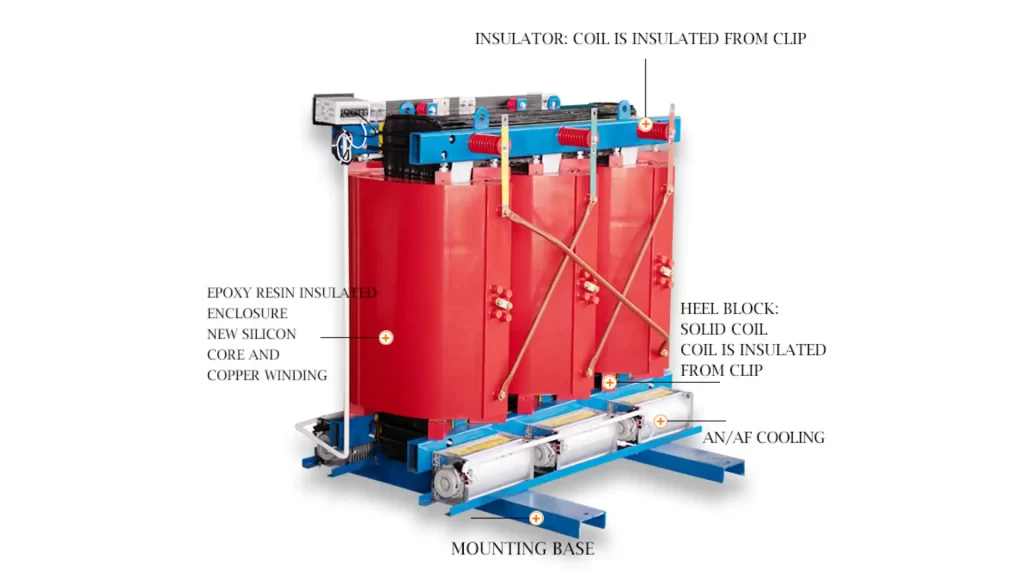
The Structural Form of Dry Type Transformer.
Open-style: This is a commonly utilized configuration, where the transformer body is directly exposed to the atmosphere. It is suitable for relatively dry and clean indoor environments (humidity should not exceed 85% at 20 degrees Celsius). Typically, it employs two cooling methods: air self-cooling and forced air cooling.
Enclosed-style: In this configuration, the transformer body is enclosed within a sealed casing, preventing direct exposure to the atmosphere. It is primarily used in mining applications due to its poor sealing and heat dissipation conditions, classified as explosion-proof.
Cast resin-type: This type of transformer utilizes epoxy resin or other resins for casting as the main insulation. It features a simple structure and compact size, making it suitable for transformers with smaller capacities.
EverNew Transformer manufactures various types of dry-type transformers, including our renowned 1000KVA open-style dry-type transformer, 2000KVA mining transformer, and 1500KVA cast resin-type dry-type transformer. For inquiries about dry-type transformers, please contact us for wholesale prices.
The Main Types of Dry Type Transformer
The Scene Cooling Methods of Dry Type Transformers
Dry type transformer utilize various cooling methods to regulate internal temperature effectively, ensuring normal operation and long-term stability. Common cooling methods include:
Air Natural Cooling (AN): This cost-effective method dissipates heat through convection and heat conduction with surrounding air. Transformer exteriors often feature heat sinks or dissipation plates to enhance surface area and heat dissipation.
Air Forced Cooling (AF): Employing external fans or built-in ducts, this method enhances heat dissipation through forced airflow. Control systems adjust airflow and heat dissipation efficiency as needed, maintaining stable temperature under varying loads.
Water Cooling: Some large-capacity or specialized dry type transformers may incorporate water cooling systems. Circulating cooling water carries away heat for more efficient dissipation, beneficial in high-power density applications or high-temperature environments.
Oil Cooling: Certain specialized designs may utilize lubricating oil around windings or core for enhanced heat dissipation. Although dry-type transformers typically don’t use insulating oil, this method can improve power density and heat dissipation efficiency, requiring regular maintenance and oil quality monitoring.
Overload Capacity of Dry Type Transformers
The overload capacity of dry type transformers is related to environmental temperature, the load condition before overload (initial load), the insulation heat dissipation condition of the transformer, and the thermal time constant. If necessary, the overload curve of dry type transformers can be obtained from the manufacturer.
Installation and Commissioning of Dry Type Transformers
Unboxing Inspection of Dry Type Transformers
Upon receiving the transformer product, it is essential to conduct an unpacking inspection. Firstly, check the packaging integrity to prevent damage during transportation. After unpacking, inspect the transformer body for any signs of external damage, displacement, or component damage. Verify if the nameplate data on the transformer matches the design requirements and ensure that all factory documents are complete. Additionally, examine the electrical support components or connection lines for any damage. Finally, cross-reference the product manual, transformer nameplate, and factory testing report to confirm compliance with design requirements. Also, check for any damaged or missing spare parts.
Transformer Installation
Firstly, inspect the foundation of the transformer to ensure the embedded steel plates are level and free from any voids underneath, ensuring the foundation possesses good seismic resistance and sound absorption properties. Any irregularities may result in increased noise levels after installation.
Next, use rollers to move the transformer to the installation position, carefully adjusting it to the designated location. Ensure the installation is level and meets the design requirements.
Finally, weld four short channel steels on the four corners closely adjacent to the transformer base to prevent any movement during operation. The transformer should be placed on a stable platform, and the embedded steel plates should be level and void-free to ensure optimal seismic resistance and sound absorption properties. The bottom of the transformer is equipped with fixed screw holes for precise adjustment to the designated position.
Wiring Methods for Dry Type Transformers
Dry-type transformers can be connected using various wiring methods, depending on the specific application and electrical requirements. Some of the common wiring methods include
Delta-Delta (Δ-Δ) connection: In this configuration, the primary and secondary windings are connected in a delta configuration. It is generally used in applications where the load is balanced and ungrounded.
Delta-Star (Δ-Y) connection: This configuration involves connecting the primary winding in a delta configuration and the secondary winding in a star (wye) configuration. It is widely used in distribution systems where the primary side is ungrounded and the secondary side is grounded.
Star-Delta (Y-Δ) connection: In this setup, the primary winding is connected in a star configuration and the secondary winding is connected in a delta configuration. It is generally used in applications where the primary side is grounded and the secondary side is ungrounded.
Star-Star (Y-Y) connection: In this setup, both the primary and secondary windings are connected in a star configuration. It is generally used in low-voltage distribution systems where grounding on both sides is critical.
Zigzag connection: This connection method involves interconnecting the primary and secondary windings in a zigzag pattern. It is often used in systems where neutral point grounding and harmonic mitigation are required.
Grounding of Dry Type Transformers
The grounding point of the dry type transformer is located on the base of the low-voltage side. There is a special grounding bolt and grounding symbol. The grounding of the transformer must be reliably connected to the protective grounding system through this point. When the transformer is equipped with a casing, the casing should be firmly connected to the grounding system. In a low-voltage system with a 3 phase four-wire structure, the neutral line should also be reliably connected to the grounding system. This not only ensures the correctness of the grounding, but also enhances the safety of electrical installation.
Transformer Pre-Operation Testing and Commissioning
Before activating the transformer for operation, thorough testing and commissioning procedures are imperative to ensure optimal performance and safety standards.
Pre-Energization Checks:
- Inspect for Loose Fasteners: Verify all fasteners are securely tightened to prevent any potential hazards during operation.
- Electrical Connection Verification: Ensure all electrical connections are correct and properly secured to guarantee reliable performance.
- Ground Insulation Distance Inspection: Check the insulation distances between components and to ground, adhering to safety standards.
- Winding and Core Inspection: Examine windings and core for any foreign objects or debris that may affect performance.
Post-Energization Procedures:
- Turns Ratio and Connection Group Verification: Confirm the transformer’s turns ratio and connection group, cross-referencing with manufacturer specifications.
- Resistance Measurement: Measure the DC resistance of high and low voltage windings to ensure they meet expected values.
- Insulation Resistance Testing: Conduct insulation resistance tests between coils and between coils and ground, comparing results with acceptable thresholds.
- Dielectric Strength Testing: Perform dielectric strength tests at prescribed voltages to assess insulation integrity and safety.
- Comparison with Factory Data: Compare test results with the manufacturer’s factory test data to validate performance and identify any discrepancies.
Pre-Operation Inspection:
- Fastener Tightness: Inspect all fasteners to ensure they remain tight and secure.
- Electrical Connections: Verify electrical connections for accuracy and reliability.
- Insulation Distance: Confirm appropriate insulation distances between live parts and ground to prevent electrical hazards.
- Foreign Object Check: Ensure no foreign objects are present near the transformer that could interfere with operation.
- Surface Cleaning: Clean the surface of windings to maintain optimal performance and prevent contamination.
Commissioning Procedures:
- Turns Ratio and Connection Group Verification: Reconfirm turns ratio and connection group alignment, ensuring compatibility with system requirements.
- Insulation Resistance Check: Validate insulation resistance levels, addressing any anomalies or deviations promptly.
- Withstand Test Compliance: Ensure all withstand tests comply with regulatory standards and safety protocols.
- Fan Functionality: If equipped with fans, verify proper operation and functionality to maintain optimal cooling efficiency.
Dry Type Transformer Trial Run
After thorough pre-operation checks, the transformer is ready for an energization trial run. During this trial period, it is essential to pay close attention to several key points:
Abnormal Sounds, Noise, and Vibrations: Monitor for any unusual sounds, noise, or vibrations emanating from the transformer, which could indicate underlying issues.
Unusual Odors: Take note of any abnormal odors, such as a burning smell, which may suggest overheating or other problems within the transformer.
Discoloration due to Local Overheating: Inspect for any signs of discoloration on the transformer, particularly in areas prone to local overheating, as this could indicate thermal issues.
Ventilation and Air Circulation: Ensure proper ventilation and air circulation around the transformer to prevent heat buildup and maintain optimal operating conditions.
In addition to these considerations, there are specific points to keep in mind:
Firstly, while dry-type transformers exhibit strong moisture resistance, they are still susceptible to moisture ingress, especially those with lower insulation levels. Operating dry-type transformers in environments with relative humidity below 70% is crucial for ensuring reliability and preventing moisture-related issues. Prolonged shutdowns should also be avoided to prevent severe moisture ingress. If the insulation resistance falls below 1000Ω/V (operating voltage), it indicates significant moisture ingress, and the trial run should be halted.
Secondly, dry-type transformers used for voltage boosting in power stations differ from oil-immersed transformers. It is prohibited to operate the low-voltage side in an open circuit to prevent insulation breakdown caused by transient overvoltages from the grid or lightning strikes on the line. To mitigate the risks of transient overvoltages, surge arresters (such as Y5CS zinc oxide surge arresters) should be installed on the voltage bus side of the dry-type transformer. Following completion of commissioning, the transformer can be energized for trial operation. During this period, focus on monitoring for abnormal sounds, noises, vibrations, and odors. Ensure proper ventilation and air exchange. If all indicators are satisfactory, the transformer can be put into long-term use.
Click me!How to Identify Faults in Dry Type Transformers
Dry type transformers are crucial components in electrical systems, providing voltage transformation without the need for insulating oil. While they are known for their reliability and safety, like any electrical equipment, they can experience faults over time. Detecting and diagnosing these faults promptly is essential to prevent downtime and ensure the continued operation of the electrical system. In this article, we’ll explore some common methods for identifying faults in dry-type transformers.
1. Visual Inspection
A visual inspection is often the first step in identifying transformer faults. Look for signs of overheating such as discoloration or burning marks on the transformer casing or windings. Check for loose connections, damaged insulation, or any foreign objects inside the transformer.
2. Thermographic Inspection
Thermographic imaging can detect hot spots within the transformer, indicating areas of potential failure. Using an infrared camera, technicians can identify temperature anomalies that may signal loose connections, overloaded circuits, or insulation breakdown.
3. Electrical Testing
- Insulation Resistance Testing: Measure the insulation resistance between windings and between windings and ground. A decrease in insulation resistance could indicate moisture ingress or insulation breakdown.
- Transformer Turns Ratio (TTR) Test: Verify the turns ratio between primary and secondary windings to ensure proper voltage transformation.
- Power Factor Testing: Evaluate the power factor to assess the condition of the insulation and identify potential faults.
- Partial Discharge Testing: Detect partial discharges within the transformer, which may indicate insulation degradation or imminent failure.
4. Acoustic Monitoring
Listen for abnormal sounds such as buzzing, humming, or cracking noises emanating from the transformer. Unusual sounds could signify loose components, mechanical stress, or electrical arcing.
5. Load Testing
Conduct load testing to assess the transformer’s performance under operating conditions. Monitor voltage levels, current flow, and temperature rise to identify any deviations from normal operating parameters.
6. Comprehensive Analysis
Integrate data from visual inspections, thermographic imaging, electrical tests, acoustic monitoring, and load testing to perform a comprehensive analysis of the transformer’s condition. Compare findings against manufacturer specifications and historical data to identify potential faults and prioritize corrective actions.
Regular inspections and testing are essential to ensure the reliability and safety of dry-type transformers. By combining visual inspections, thermographic imaging, electrical testing, acoustic monitoring, and load testing, technicians can effectively identify and address faults before they escalate into major issues, thereby minimizing downtime and extending the transformer’s lifespan. Remember, early detection is key to preventing costly repairs and unplanned outages. Join EverNew Transformers today for professional transformer testing support.
Click me!Conclusions
The above is an introduction to dry type transformers. Dry type transformers are versatile electrical equipment widely used across various applications. If you have any procurement needs or related inquiries, please feel free to contact us. EverNew, as a leading transformer manufacturer in China, exports a wide range of transformers globally every year. We have extensive experience in power consulting, construction, maintenance, and after-sales service.
Click me!